Case Studies
Mercedes Benz U.S. International
Industry: Automotive
Solution: Value-Added Services
GAA Company: ARD Logistics
Unique Solution:
Reduced Takt Time by 23% - with No Labor or Cost Increase
Mercedes Benz U.S. International (MBUSI) is known throughout the world for exceptional quality - with a production system that's based on automotive Best Practices from multiple countries. MBUSI vehicles set the standard in the industry. The partners they select must meet the highest quality expectations and deliver innovative solutions that are safe, efficient, predictable and dependable.
Those are just a few reasons we're proud of our 20-year relationship with this exceptional corporation.
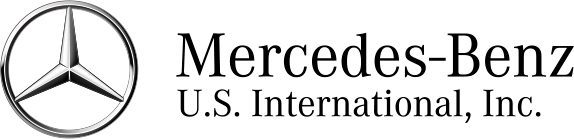
Challenge
ARD Logistics - part of the GAA Family of Companies - was selected to help MBUSI reduce the takt time of their car assembly A1 from 180 to 138 seconds per vehicle. ARD managed the current shopping cart cell, staffed with six team members, which had to be designed and restaffed to meet this goal.
The previous process required multiple material moves across a major traffic aisle, these were considered highly-congested moves. Every step of the process needed to be scrutinized in order to create a better way and significantly reduce taky time.
Solution
Our position with MBUSI is unique in that ARD operates from within the MBUSI Logistics Center in their Tuscaloosa County plant in Alabama. Because our team was physically there, we were able to approach this challenge from a unique perspective and bring a wealth on real-world experience to designing a solution that not only reaches the stated goal, but also lives up the MBUSI's stringent quality expectations.
The ARD Team got it done.
ARD Logistics designed an innovative process and achieved the targeted 23% reduction in takt time - successfully reducing it from 180 to 138 seconds per vehicle.
The new layout included with the new process created safe aisle widths and improved tugger delivery, forklift delivery and eliminated team member rack exchanges.
In addition, new storage locations defined within the new process will provide more ergonomic picks for team members.
With the new layout, ARD was able to increase efficiencies for the forklift driver by reducing traffic congestion. Finally, the solution also reduced the requirement for the tugger route by 2.5 replenishments per hour.
Solution Highlights
- ARD Engineers redesigned the work cell and relocated parts in the shopping cart to minimize traffic aisle
- The newly-created process increased pick frequency of assembly line AGV carts to 122 seconds to maintain an essential buffer for the shopping cart.
- The process redesign streamlined airduct picking process - improving sequence racks swap and implemented a change to flow rack picking.
- We eliminated the front carpet SLT racks on tugger delivery and implemented a change to flow rack picking, which created a "Safe Staging Area" for transfer of racks from dollies to floor staging.
In addition to providing a World-Class Solution that met their goals, we were able to add value as an MBE - helping MBUSI meet their commitment to supplier diversity. As stated on their website: